November 14, 2018 feature
Stretchable thermoelectric coils for energy harvesting in miniature flexible wearable devices
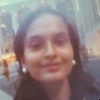
Thamarasee Jeewandara
contributing writer
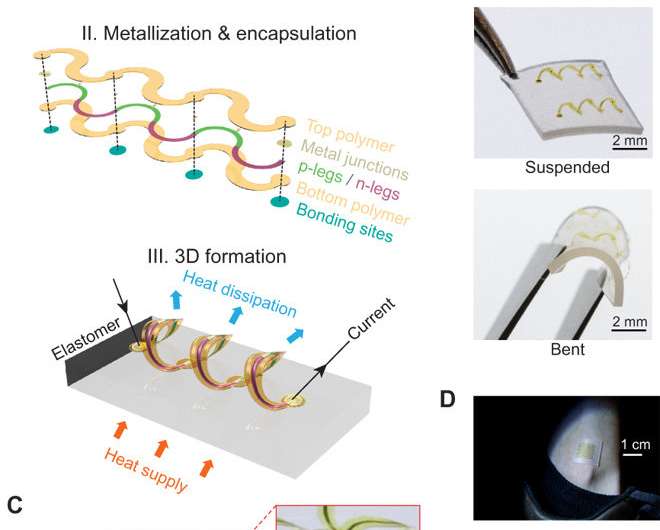
Miniaturized semiconductor devices with energy harvesting features have paved the way to wearable technologies and sensors. Although thermoelectric systems have attractive features in this context, the ability to maintain large temperature differences across device terminals remains increasingly difficult to achieve with accelerated trends in device miniaturization. As a result, a group of scientists in applied sciences and engineering has developed and demonstrated a proposal on an architectural solution to the problem in which engineered thin-film active materials are integrated into flexible three-dimensional (3-D) forms.
The approach enabled efficient thermal impedance matching, and multiplied heat flow through the harvester to increase efficient power conversion. In the study conducted by Kewang Nan and colleagues, interconnected arrays of 3-D thermoelectric coils were built with microscale ribbons of the active material monocrystalline silicon to demonstrate the proposed concepts. Quantitative measurements and simulations were conducted thereafter to establish the basic operating principles and key design features of the strategy. The results, now published on Science Advances, suggested a scalable strategy to deploy hard thermoelectric thin-films within energy harvesters that can efficiently integrate with soft material systems including human tissue to develop wearable sensors in the future.
Thermoelectric devices provide a platform to incorporate ubiquitous thermal gradients that generate electrical power. To operate wearable sensors or the "Internet of Things" devices, the temperature gradient between the surrounding environment and the human body/inanimate objects should provide supplies. Continued advances in the field focus on aggressive downscaling of power requirements for miniaturized systems to enhance their potential in thermoelectric and energy harvesting applications. Integrated processors and radio transmitters for example can operate with power in the range of subnanowatts, some recent examples are driven via ambient light-based and . Such platforms can be paired with sensors with similar power to enable distributed, continuous and remote environmental/biochemical monitoring.
Two key challenges in the development of miniaturized thermoelectric harvesters include matching the requisite thermal impedance and mechanical compliance of the active materials to integrate in biological systems. A well-developed system for includes combining thin film polymers with metal foils such as wires or ribbons. In the study, Nan et al propose and demonstrate a solution by developing a two-dimensional (2-D) precursor system in the development of functional 3-D helical coils. The naturally flexible nature of the coils enabled the systems to conform to complex biological surfaces, even those dynamic with time, to ensure excellent thermal contact with the heat source. Furthermore, the 3-D nature of the system provided a multifold increase in the surface area for higher heat exchange capacity to yield maximum power.
The thermoelectric helical coil architecture was fabricated using monocrystalline silicon as the active material. The mechanically guided assembly generated 3-D helical structures from 2-D serpentines via compressive buckling. The serpentines incorporated silicon ribbons with p- and n-type segments, and the system was encapsulated on the top and bottom with polymer coatings. The architecture enabled transformation of the system from 2-D to 3-D during deployment and use. Although , the 3-D coils were able to provide remarkable levels of mechanical compliance and robustness during handling and bending applications. The assembly did not significantly deviate from the geometry predicted using finite element analysis (FEA). Such material characteristics made the system well-suited to form intimate thermal interfaces to the human body, such as the wrist or ankles.
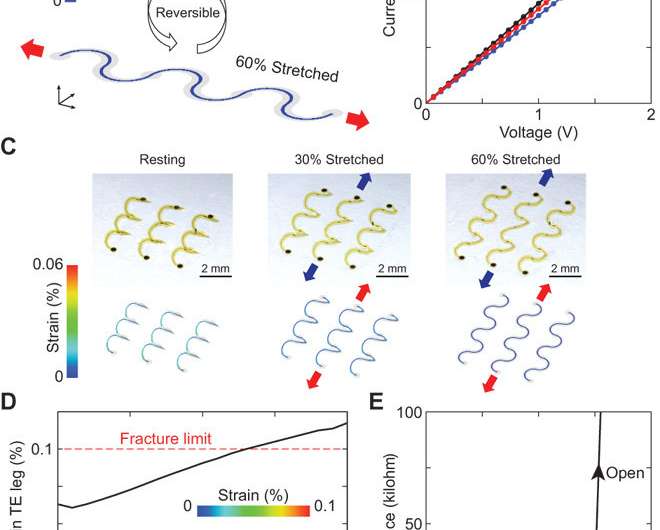
To improve mechanical and thermal properties of the 3-D coils, the scientists used FEA software for computationally guided optimization of the resulting device. , the 3-D architecture of the device was advantageous for effective harvesting. Therefore, by design, the 3-D helical coil system included a tapering geometry that increased in width toward the top as engineered using FEA to optimize thermal and mechanical responses. The design scheme in the study was enhanced specifically for harvesting in miniature devices. Increased cooling capacity of the device design had greater benefits to contrast any losses owing to parasitic heat flow in the system.
Nan et al, also conducted mechanical compliance tests on the devices to understand their capacity to endure substantial bending, in-plane stretching and out-of-plane compression, as with . The 3-D structures could be stretched by up to 60 percent in the in-plane direction for hundred cycles and vertically compressed up to 30 percent, with minimal degradation in electric properties. The devices showed exceptional mechanical compliance as predicted by FEA. Uniaxial stretching across 200 cycles did not result in electrical or mechanical failure. The 3-D coil showed resilience with potential for interfacial integration within miniature devices.
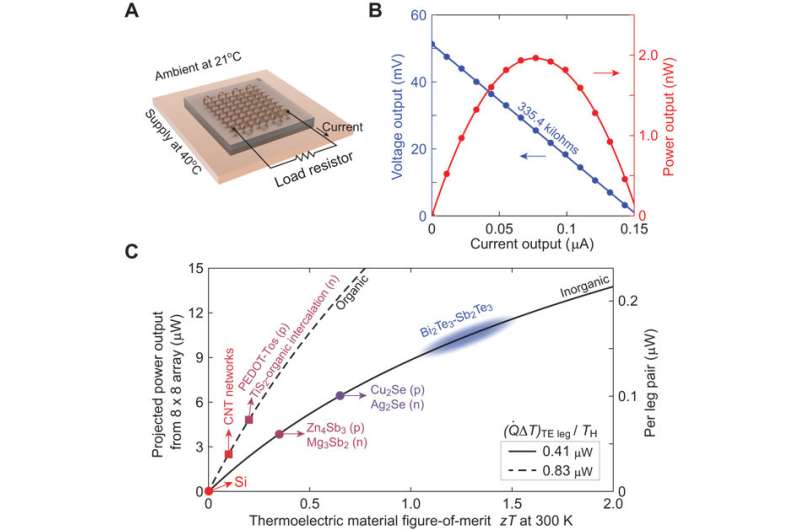
Power output projections of the harvesting devices were also characterized to show consistent results aligned with design expectations. The open-circuit voltage of the device did not diminish across time in the measurements indicating that the thermal profile of the device was in a steady state. In the study, the authors generated a road map for power enhancement and a fabrication scheme to engineer energy harvesting devices with materials other than silicon – including organic variants.
The authors recommend additional research on deposition methods, doping and patterning for organic and composite materials. The materials should not succumb to electrical resistance during mechanical transformation from 2-D to 3-D. With silicon used in the study, a three-fold increase in resistance was observed during the transformation potentially due to electrode contact, device degradation or plastic deformation in some parts of the device. The study represents a promising strategy to integrate thin-film materials in harvesters with soft material systems (including human skin) to realize energetically optimized wearable electronic devices in the future.
Written for you by our author —this article is the result of careful human work. We rely on readers like you to keep independent science journalism alive. If this reporting matters to you, please consider a (especially monthly). You'll get an ad-free account as a thank-you.
More information: Kewang Nan et al. Compliant and stretchable thermoelectric coils for energy harvesting in miniature flexible devices, Science Advances (2018).
U. Pelz et al. Fabrication Process for Micro Thermoelectric Generators (μTEGs), Journal of Electronic Materials (2015).
Chunlei Wan et al. Flexible thermoelectric foil for wearable energy harvesting, Nano Energy (2016).
Patrick P Mercier et al. Energy extraction from the biologic battery in the inner ear, Nature Biotechnology (2012).
Journal information: Science Advances , Nature Biotechnology , Nano Energy
© 2018 Science X Network