August 14, 2019 feature
Metal-oxide semiconductor nanomembrane-based multifunctional electronics for wearable-human interfaces
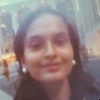
Thamarasee Jeewandara
contributing writer
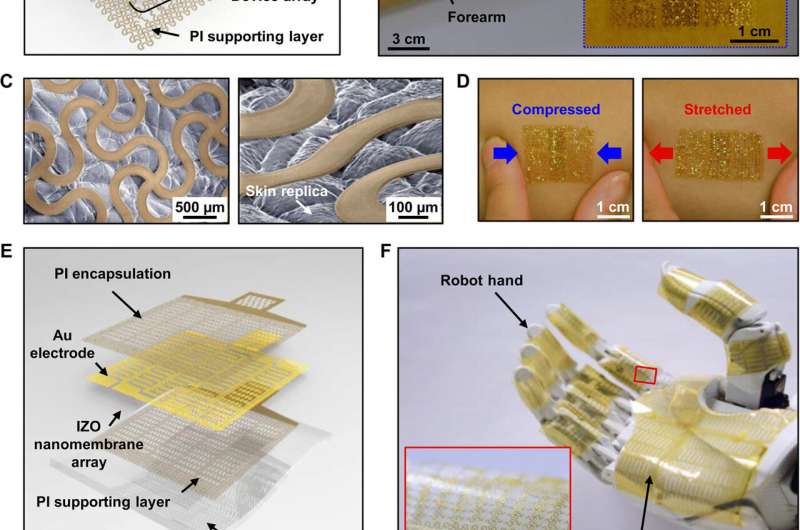
Wearable electronic human-machine interfaces (HMIs) are an emerging class of devices to facilitate human and machine interactions. Advances in electronics, materials and mechanical designs have offered pathways toward commercial wearable HMI devices. However, existing devices are uncomfortable since they restrict the human body's motion with slow response times and challenges to realize multiple functions. In a recent report on Science Advances, Kyoseung Sim and an interdisciplinary research team in materials science and engineering, mechanical engineering, biomedical engineering, electrical and computer engineering in the U.S. and China, detailed the development of a novel polymer.
In the work, they engineered a sol-gel-on-polymer-processed indium zinc oxide semiconductor nanomembrane-based ultrathin stretchable electronics device. The advantages included multifunctionality, simple manufacturing processes, imperceptible wearing and robust interfacing. The multifunctional wearable HMI devices ranged from resistive random-access memory (ReRAM) for data storage to form field-effect transistors (FETs) that interfaced with switching circuits. Additional functionalities included sensors for health and body motion sensing, and micro-heaters to deliver temperature. After testing the individual components for their unique properties, Sim et al. engineered the HMI devices as seamless wearables for humans and also as prosthetic skin for robots to offer intelligent feedback and form a closed-loop HMI (human-machine interface) system.
Wearable human-machine interfaces (HMIs) function as direct communication pathways between humans and machines. The interfaces can sense physical or electrophysiological parameters from the wearers and facilitate the machines to perform corresponding functions. Recent developments in electronics, materials and mechanical designs have advanced HMI devices. Such wearables are, however, still semisoft and uncomfortable for seamless integration due to inability to deform and adapt to a range of dynamic human movements. Soft electronic materials that perfectly match the requirements of interest offer an alternative to construct the stretchable, wearable HMI devices. However, the soft rubbery materials have featured to undergo substantial hysteresis upon cyclic deformation. Comparatively, inorganic materials can and undergo substantial hysteresis for adoption as wearable electronics and sensors.
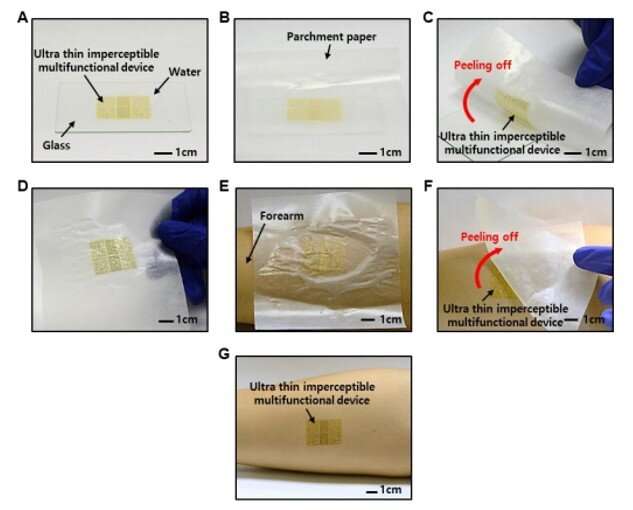
Unique material properties can facilitate and to serve as key enablers for HMI devices with soft and stretchable character. To achieve multiple functions including sensing, switching, stimulation and data storage, however, researchers must still develop diverse types of electronic functional materials, alongside heterogeneous integration technologies, such as . Such devices are associated with complex fabrication procedures, incompatibility of engineering, low scalability and high cost. Additionally, to team human and machine interfaces, materials scientists require broader understanding of the parameters on interaction, evaluation and communication. Wearable HMI devices are therefore required on both humans and machines to effectively form closed-loop pathways. As a result, research in the field of is aimed at developing wearable HMI devices to close the existing gaps in technology.
In the present work, Sim et al. developed an ultrathin, mechanically imperceptible and stretchable HMI device to be worn on human skin and on a robot, to capture physical data and offer intelligent feedback respectively, to create a closed-loop HMI system. They developed the materials without combining multiple functional materials, devices or excessive heterogeneous steps of integration. The device design on the ultrathin, meandering, open-mesh configuration with mechanical stretchability allowed the user to be fully unaware of the device, while it extracted useful signals of the user. The wearable device collected signals from the human muscle to guide the robot directly to allow the user to feel the sensations experienced by the robot hand. The research team collectively studied the materials and device design, fabrication and characterization to demonstrate fundamental aspects of the metal oxide nanomembrane for multifunctional applications in HMI devices.

Sim et al. composed the HMI device with an (IZO) nanomembrane-based ReRAM (random-access memory) array, FET (field-effective transistor) array, distributed temperature sensors, UV sensors, strain sensors and gold (Au)-based thermal simulators. They engineered all devices on a thin (~2 µm) polyimide (PI) layer by spin coating on top of a rigid glass holding substrate to allow the easy release of the device to be freestanding. After many intricate engineering steps, they completed the device fabrication by immersing it in buffer oxide etchant (BOE) to release the device from the glass platform. Using parchment paper, the scientists then transferred the device on to a human arm without an additional adhesive. They used to show that the skin polymer did not undergo delamination upon contact with skin. To form a closed-loop HMI system between human and machine, the scientists similarly developed a prosthetic skin composed of (PDMS) and an array of sensors to mimic sensory functions of the human skin and implemented it onto a robot hand.
Sim et al. performed detailed characterization of the sol-gel-on-polymer-processed IZO nanomembrane oxide semiconductor, which was key to realize multiple functionalities without heterogenous integration. Since data storage devices such as memory were integral components in wearable HMIs; the scientists constructed the IZO-nanomembrane-based stretchable ReRAM with an Au/IZO/Au sandwiched structure with PI (polyimide) encapsulation. Under sufficient voltage, they created oxygen ions and oxygen vacancies to form a conductive filament across the two electrodes for drastic current transition from high resistance state (HRS) to low-resistance state (LRS). When they applied a reverse bias at a specific voltage, the oxygen vacancies became neutralized, causing the conductive filament to rupture and for the current to decrease drastically. Sim et al. performed (WRER) cycles and retention tests to assess the reliability of the IZO nanomembrane-based ReRAM, where the results showed stable operation without degradation.
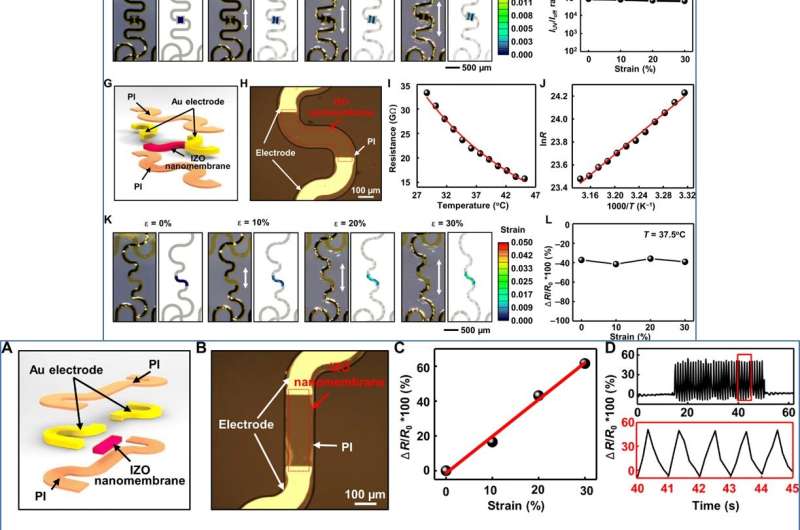
They confirmed the mechanical strain effect on device performance by testing the ReRAM under different levels of mechanical stretching using a custom-made stretcher. The results showed that the semiconductor experienced minimal and negligible strain when stretched, reflecting the rational design of the device. The results indicated the ability of the ReRAM device to function stably under mechanical strain without substantial degradation. The FET used in the device similarly formed a fundamental building block to interface and switch electronics for HMIs.
The scientists then tested the ultrathin UV sensor of the skin-wearable polymer and its ability to monitor UV exposure for applications to . Similarly, they tested the effects of skin temperature, by measuring the resistance of the ultrathin stretchable thermistor at different temperatures. They calculated the temperature coefficient to be comparable to . The research team also developed an IZO nanomembrane-based strain sensor for communication between a human and robot to highlight the versatility of the IZO material. Sim et al. compared the experimental results with finite element analysis (FEA) to compute the strain profile of the IZO sensing area under different levels of mechanical stretching. The simulations agreed well with the experimental results.
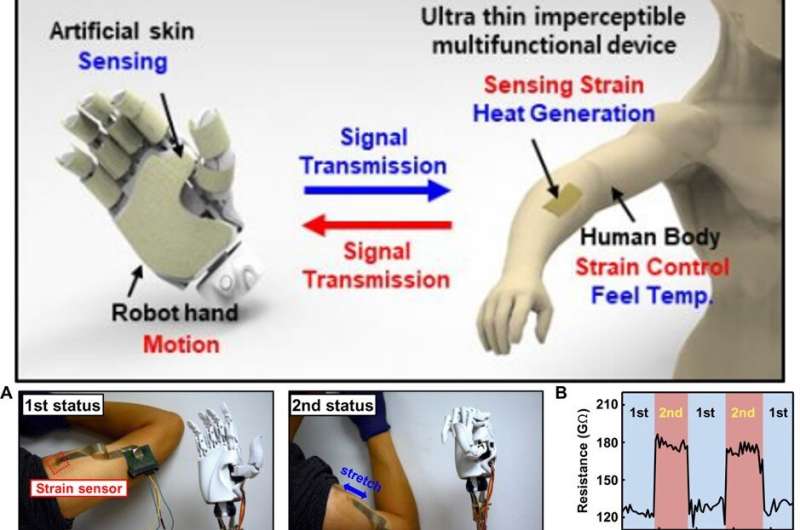
After testing the individual functions of the multifunctional device, Sim et al. demonstrated the multifunctionality of the closed-loop interactive HMIs. When wearable sensors on the human skin detected signals such as strain induced human motion, the detected signals could control the motion of the robotic hand. For instance, when the research team placed the IZO strain sensor on the human shoulder it detected strain by motion of the human arm or when the user grasped an object. In parallel, the prosthetic skin based on the IZO temperature sensor of the robotic hand detected the temperature of the external environment or of the grasped object to determine the apt voltage to apply to a soft thermal stimulator on the human skin to transmit the sensation. On the basis of a series of such cordinated interactions, the scientists created an interactive closed-loop HMI system.
In this way, Kyoseung Sim and colleagues engineered a sol-gel-on-polymer processed IZO metal oxide nanomembrane and exhibited its versatility relative to ultrathin soft memory devices, transistors, temperature sensors, strain sensors and UV sensors. They formed the multifunctional device simultaneously in a single step process without any heterogenous integration. The combined ultrathin stretchable electronics-enabled wearable sensors, prosthetic skin and actuator device for human-robot interfaces proved the feasibility of the closed-loop HMI system. Such a setup will pave the way to cost-effective, scalable manufacturing and wearable HMI devices capable of seamless integration with the user. The scientists envision that the wearable HMI will become a vital technology with enhanced capabilities, comfort and convenience for effective teaming between machines and humans.
Written for you by our author —this article is the result of careful human work. We rely on readers like you to keep independent science journalism alive. If this reporting matters to you, please consider a (especially monthly). You'll get an ad-free account as a thank-you.
More information: Kyoseung Sim et al. Metal oxide semiconductor nanomembrane–based soft unnoticeable multifunctional electronics for wearable human-machine interfaces, Science Advances (2019).
Donghee Son et al. Multifunctional wearable devices for diagnosis and therapy of movement disorders, Nature Nanotechnology (2014).
D.-H. Kim et al. Stretchable and Foldable Silicon Integrated Circuits, Science (2008).
Journal information: Science Advances , Nature Nanotechnology , Science
© 2019 Science X Network