June 22, 2022 feature
Upcycling plastics through dynamic cross-linking
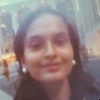
Thamarasee Jeewandara
contributing writer
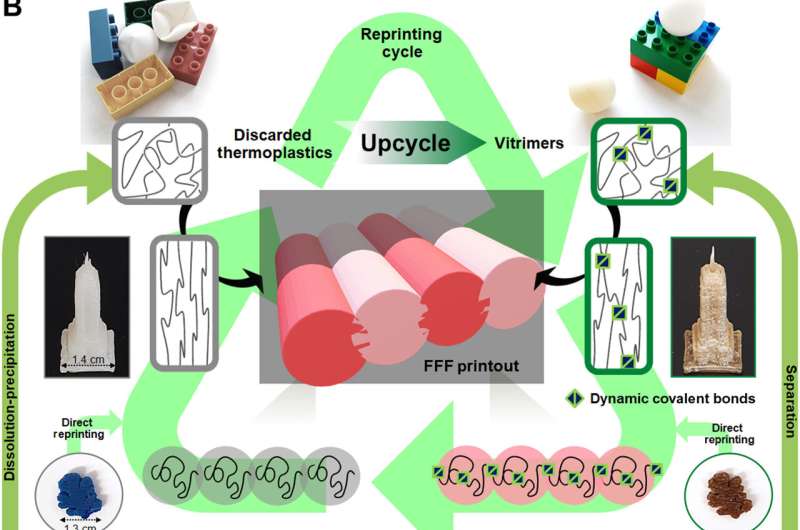
If bioengineers can upcycle commodity plastics into higher-performance materials, they can establish sustained closed-loop manufacturing with broader industrial and environmental benefits. For example, upcycled plastics can be reprocessed to form custom-designed structures via an energy-resource-efficient additive manufacturing circuit based on (the FFF method). In a new report now published in Science Advances, Sungjin Kim and a team of researchers in chemistry, materials science and interdisciplinary research at the Oak Ridge National Laboratory and the University of Tennessee, U.S., introduced a circular model to upcycle a prominent thermoplastic known as (ABS). The team upcycled the material into a recyclable and robust covalent network, reprintable via fused filament fabrication. The process overcame major challenges of reprinting cross-linked materials to produce strong, tough and solvent-resistant 3D objects separate from unsorted plastic waste. The outcomes provide an adaptable approach for advanced manufacture of circular plastics.
A circular plastic economy
Plastic production has reached in 2013 to a projected 16% of the net global carbon emission by 2050. As a best-case scenario, researchers therefore aim to increase plastic recycling to reduce the production demand growth and . By establishing a closed-loop circulation of plastics, they can achieve net-zero carbon emission to develop manufacturing paths of plastics for the best possible outcomes. Of the existing manufacturing methods, additive manufacture provides 3D materials production on demand to convert plastic wastes into useful 3D constructs with better material performance and thereby uphold . The team incorporated the method of fused filament fabrication for its user-friendly and . In this work, Kim et al converted acrylonitrile butadiene styrene (abbreviated as ABS) into a by using the technique of .
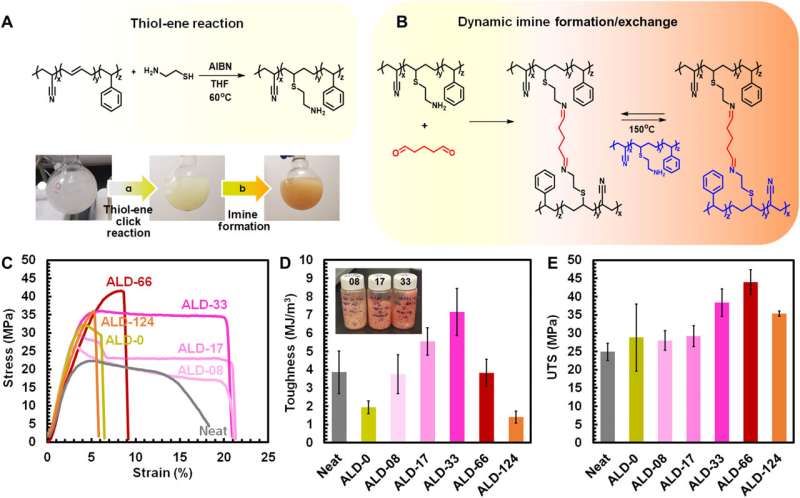
Developing vitrimers: An exciting class of renewable plastics
In order to upcycle commodity plastics for reprinting applications, the researchers replaced existing methods of developing cross-linked networks with reversible bonds. Kim et al accomplished this via . By upcycling ABS to the ABS vitrimer (a class of renewable plastics), they notably improved the thermomechanical and chemical robustness of the material. The vitrimer showed multipath recyclability, alongside improved interfilament bonding and solvent resistance. They deconstructed the vitrimer wastes via dissolution and reprinted them using the full-filament fabrication method to form useful 3D structures, dissolving and upcycling plastics in a value-enhancing cycle. The process reduced carbon-dioxide equivalent emissions by at least 65% , representing a readily adaptable circular plastics manufacturing approach.
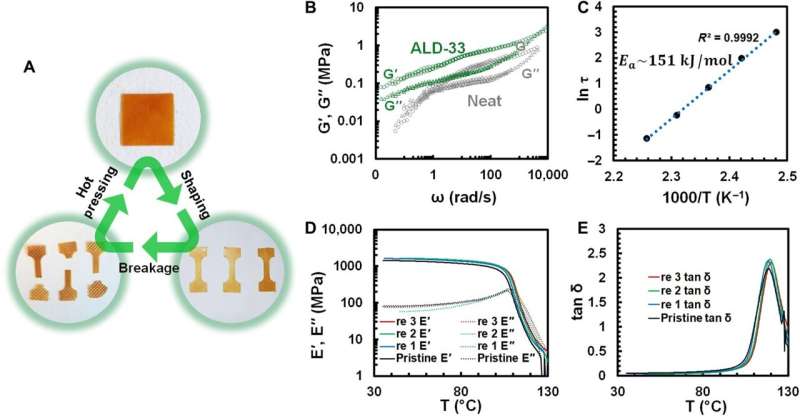
One-step modification and multiple steps of product characterization
In this way, Kim et al upcycled the ABS to a FFF-printable vitrimer in which the initial compound was ductile and tough with unsaturated double bonds that could be amended post-functionalization. The team then implemented to functionalize constituents of the construct, to produce the ABS-vitrimer. They observed the reactions via and . The products were solvent-resistant for a range of solvents, including acetone chloroform, to tetrahydrofuran and . The scientists assessed the mechanical properties of the constructs via tensile tests, alongside viscoelasticity and processability at higher temperatures, while improving thermomechanical stability of the products.
Recyclability of plastic products and the process of full filament fabrication (FFF)
The research team determined the recyclability of the product via and tensile tests on the samples, where the outcomes showed nearly identical storage moduli for four individual samples after three recycles to indicate good recoverability of elasticity. The scientists also showed the possibility of reprocessing cross-linked ABS-vitrimer; to recycle them by reheating without using solvents or additives to dissociate the network and enable reprintability.
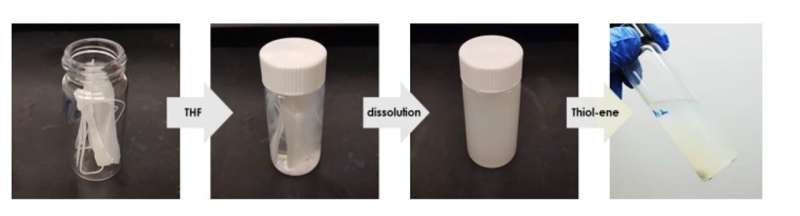
The FFF method
The FFF method of vitrimer printability enabled fast exchange kinetics and malleability with mechanical integrity to develop self-standing structures. The method allowed improved interlayer integration for enhanced strength. When Kim et al immersed the product in tetrahydrofuran, the samples were solvent resistant, indicating crosslinking throughout the layered structure. The technique led to easy sample separation from waste mixtures for ready recycling and upcycling processes. The scientists noted superior for the bioinspired upcycled ABS-vitrimers, conferring enhanced structural strength with reduced materials consumption during the manufacturing process compared with conventional routes. The work emphasized the possibility of developing FFF-printable vitrimers and composites for applications across robotics, electronics and therapies in biomedicine.
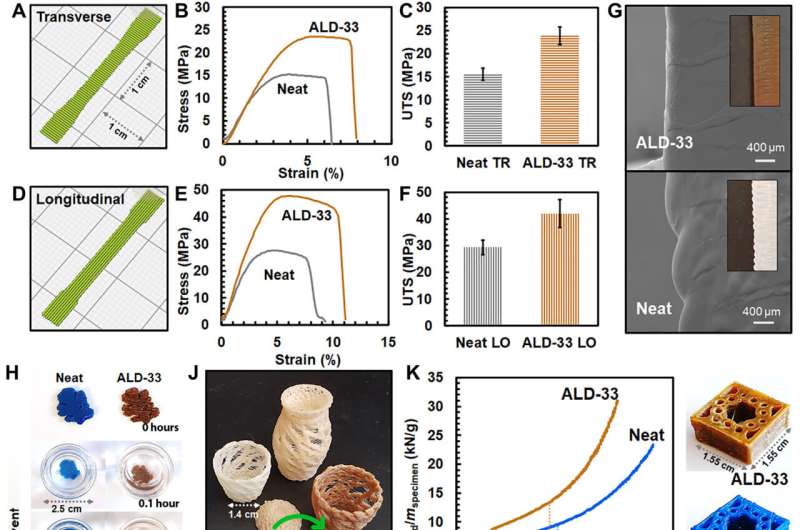
Outlook: Recyclable plastics for sustainability
In this way, Sungjin Kim and colleagues presented their findings to upcycle waste plastics into elaborate 3D-printed, robust and recyclable cross-linked materials. The strategy applies to commodity thermoplastics to establish multiple value-enhancing circular models. This approach of using an additive manufacturing method to upcycle commodity plastics to develop materials with higher-value structures provides a commercially and environmentally viable strategy for adoptable closed-loop circular manufacture. The results of upcycling plastics will have significant long-term impacts in industrial applications, health care and provide a robust environmental strategy.
Written for you by our author —this article is the result of careful human work. We rely on readers like you to keep independent science journalism alive. If this reporting matters to you, please consider a (especially monthly). You'll get an ad-free account as a thank-you.
More information: Sungjin Kim et al, Closed-loop additive manufacturing of upcycled commodity plastic through dynamic cross-linking, Science Advances (2022).
Peter R. Christensen et al, Closed-loop recycling of plastics enabled by dynamic covalent diketoenamine bonds, Nature Chemistry (2019).
Journal information: Nature Chemistry , Science Advances
© 2022 Science X Network