Heat and smart mixing boost enzymatic recycling of unsortable polyester plastics
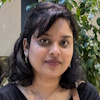
Sanjukta Mondal
contributing writer
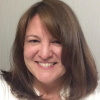
Lisa Lock
scientific editor

Andrew Zinin
lead editor

Polyester plastics, commonly found in synthetic textiles and plastic components of home appliances, are notoriously difficult to recycle. In a study recently in the Proceedings of the National Academy of Sciences, researchers from France unveiled a clever method for breaking down polyester waste into reusable building blocks using heat and leveraging the residual catalysts embedded within the plastic during the manufacturing process, eliminating the need for tedious sorting.
Sorting plastic waste is recommended before disposal in order to make the recycling process easier. Recycling of PET or polyethylene terephthalate, which is widely used in bottles, textiles, packaging, and engineering plastics, significantly benefits from this practice. Recyclers simply need to collect, separate it from other waste, and break it down via enzyme-catalyzed depolymerization into monomers, which can then be used for the next batch of PET products.
This form of recycling becomes particularly challenging with polyesters, such as polytrimethylene terephthalate (PTT) and polybutylene terephthalate (PBT), as well as PET fibers. When used in consumer products, these plastics often contain a mix of different monomers and additives such as dyes or plasticizers, making the waste difficult to sort and separate. Additionally, their rigid crystalline structures prevent the enzymes used in recycling from breaking down the plastic, as the polymer chains are packed too tightly and cannot be accessed.
In this study, researchers reported a new technique for degrading such plastic waste, which includes intentionally mixing various types of polyester waste in controlled proportions and then melting it by raising the temperature to 270°C. The residual catalysts, such as antimony trioxide, left over from the polyester manufacturing process, enabled transesterification —a chemical reaction in which the alkoxy group of an ester compound is replaced by an alcohol—leading to copolymers with random network structures.

For polyester wastes rich in fast-crystallizing polymers like PBT, melt transesterification alone failed to provide the desired results. To counter this, the researchers introduced vitrimerization—the addition of an epoxy cross-linking agent to the mix—to further slow down the crystallization time. These processes yielded a reactive mixture that crystallized at a slower rate when cooled in ice baths, resulting in a polymer structure susceptible to enzymatic attack.
The solid material obtained after the cooling process was ground up and treated with the same enzymes used for recycling semi-crystalline PET bottles. The result was high-quality monomeric building blocks suitable for manufacturing new polyester products.
The researchers highlighted that mixing PET nonwoven waste with PBT increased the enzymatic depolymerization yield from 20% for PET and 1% for PBT to 90% as a mixture. Although counterintuitive, this study establishes that blending rather than sorting might be a more viable and less tedious approach to recycling polyester waste.
Written for you by our author , edited by , and fact-checked and reviewed by —this article is the result of careful human work. We rely on readers like you to keep independent science journalism alive. If this reporting matters to you, please consider a (especially monthly). You'll get an ad-free account as a thank-you.
More information: Hernan Garate et al, Reactive mixing enables enzymatic depolymerization of recalcitrant or unsortable polyester wastes, Proceedings of the National Academy of Sciences (2025).
Journal information: Proceedings of the National Academy of Sciences
© 2025 Science X Network