New 3D-printed titanium alloy offers greater strength at lower production cost
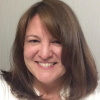
Lisa Lock
scientific editor

Andrew Zinin
lead editor

Engineers from RMIT University have produced a new type of 3D-printed titanium that's about a third cheaper than commonly used titanium alloys.
The team used readily available and cheaper alternative materials to replace the increasingly expensive vanadium.
RMIT has filed a provisional patent on their innovative approach, which has also been in Nature Communications, as the team considers commercial opportunities to develop the new low-cost approach for the aerospace and medical device industries.
RMIT's Center for Additive Manufacturing (RCAM) Ph.D. candidate and study lead author Ryan Brooke said testing of their alloy showed improved strength and performance compared to standard 3D-printed titanium alloys (Ti-6Al-4V).
Brooke, who has just accepted a Research Translation Fellowship at RMIT to investigate the next steps in commercializing the technology, said the area of 3D-printed titanium alloys was ripe for innovations.
"3D printing allows faster, less wasteful and more tailorable production, yet we're still relying on legacy alloys like Ti-6Al-4V that don't allow full capitalization of this potential. It's like we've created an airplane and are still just driving it around the streets," he said.
"New types of titanium and other alloys will allow us to really push the boundaries of what's possible with 3D printing and the framework for designing new alloys outlined in our study is a significant step in that direction."
The latest study outlines a time- and cost-saving method to select elements for alloying, to take advantage of emerging 3D-printing technology.
This work provides a clearer framework for predicting the printed grain structure of metallic alloys in additive manufacturing.
It has already been used to achieve impressive results: the team's alloy, while not presented in the study for commercial reasons, is 29% cheaper to produce than standard titanium.
Through this design framework, the metal also prints more evenly, avoiding the column-shaped microstructures that lead to uneven mechanical properties in some 3D-printed alloys.
"By developing a more cost-effective formula that avoids this columnar microstructure, we have solved two key challenges preventing widespread adoption of 3D printing," said Brooke, who recently completed market validation as part of CSIRO's ON Prime program, talking to aerospace, automotive and MedTech industry representatives about their needs.
"What I heard loud and clear from end users was that to bring new alloys to market, the benefits have to not just be minor incremental steps but a full leap forward, and that's what we have achieved here," he said.
"We have been able to not only produce titanium alloys with a uniform grain structure, but with reduced costs, while also making it stronger and more ductile."
Study corresponding author Professor Mark Easton said RCAM was focused on creating new collaborations to further develop the technology.
"We are very excited about the prospects of this new alloy, but it requires a team from across the supply chain to make it successful. So, we are looking for partners to provide guidance for the next stages of development," he said.
Samples were produced and tested at RMIT's cutting-edge Advanced Manufacturing Precinct.
More information: Ryan Brooke et al, Compositional criteria to predict columnar to equiaxed transitions in metal additive manufacturing, Nature Communications (2025).
Journal information: Nature Communications
Provided by RMIT University