New device converts plastic waste into fuel using catalyst-free pyrolysis
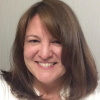
Lisa Lock
scientific editor

Andrew Zinin
lead editor

As tons of plastic waste continue to build up in landfills every day, Yale researchers have developed a way to convert this waste into fuels and other valuable products efficiently and cheaply. The results are in Nature Chemical Engineering.
Specifically, the researchers are using a method known as pyrolysis, a process of using heat in the absence of oxygen to molecularly break materials down. In this case, it's used to break plastics down to the components that produce fuels and other products. The study was led by Yale Engineering professors Liangbing Hu and Shu Hu, both members of the Center for Materials Innovation and Yale Energy Sciences Institute.
Conventional methods of pyrolysis often use a catalyst to speed up the chemical reactions and achieve a high yield, but it's a method that comes with significant limitations.
"Whenever you talk about catalysts, they're very expensive and you have a lifetime issue because catalysts will eventually die by different means," said Liangbing Hu, the Carol and Douglas Melamed Professor of Electrical & Computer Engineering & Materials Science, and director of Center for Materials Innovation.
Methods that don't employ a catalyst, though, tend to have low rates of converting the waste into products of use.
For this project, the researchers found a way around both of these obstacles and developed a highly selective, energy-efficient, and catalyst-free pyrolysis method that can convert plastic into valuable chemicals.
The key, they say, is a 3D-printed electrically heated carbon column reactor made of three sections of decreasing pore size. The first section is made of one-millimeter pores, while the next section contains 500-micrometer pores, and the third section is made of 200-nanometer pores.
As the chemicals pass through the reactor, the hierarchical porous structure plays a pivotal role in controlling the reaction progress of the chemicals. For one thing, it prevents larger molecules from advancing through the reactor before they've been adequately broken down.
Further, it provides a way to control the temperature in the reactor, which prevents coking and other effects that can inhibit the process.
To test the system, the researchers tried the reactor out on a sample of common plastic known as polyethylene. The results are impressive: They report a record-high yield of nearly 66% of the plastic waste converted into chemicals that can be used for fuels.
Using 3D printing to build the structure allowed the researchers to precisely control the dimensions of the reactor pores and investigate the effects of pyrolysis.
To demonstrate a more scalable design, the researchers also used a device made up of commercially available carbon felt. They found that this design—even without the optimization that a 3D-printed structure provided—still improved the selectivity of the pyrolysis products and achieved a satisfactory yield, converting more than 56% of the plastic into useful chemicals.
"These results are very promising and show a great potential for putting this system into real-world application and offering a practical strategy for converting plastic waste into valuable materials," said Shu Hu, assistant professor of chemical & environmental engineering.
More information: Ji Yang et al, Selective electrified polyethylene upcycling by pore-modulated pyrolysis, Nature Chemical Engineering (2025).
Journal information: Nature Chemical Engineering
Provided by Yale University